Understanding the Basics: General Process Terms in Plastic Injection Moulding
- josh61940
- Aug 9, 2024
- 3 min read
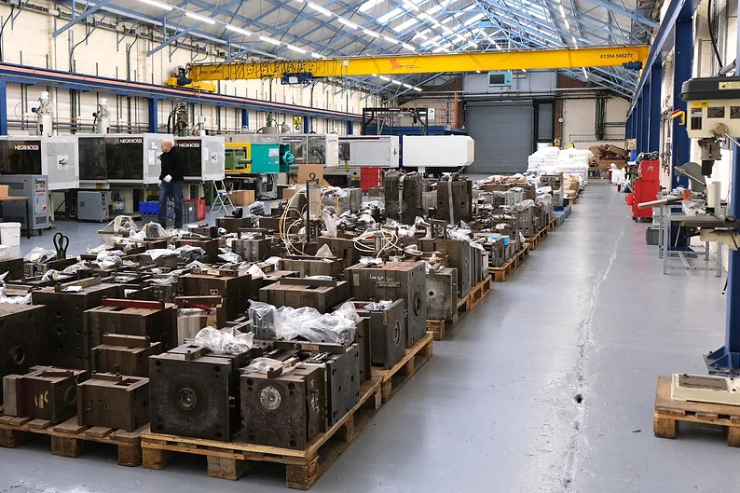
At Amey Plastics, we pride ourselves on providing top-quality plastic injection moulding services and advice to the UK manufacturing sector. To help our clients and those interested in the industry, we are launching a blog series to explain various moulding terms. In this first post, we will cover general process terms that are fundamental to understanding plastic injection moulding. We hope you find it helpful!
Injection Moulding
Injection moulding is a manufacturing process used to produce parts by injecting molten material into a mould. It is widely used for producing plastic parts, from small components to large items. The process involves feeding raw plastic material into a heated barrel, mixing and forcing it into a mould cavity where it cools and hardens into the desired shape.
Cycle Time
Cycle time is the total time required to complete one cycle of the injection moulding process, including the closing of the mould, injection of the plastic, cooling and ejection of the final part. Optimising cycle time is crucial for efficient production and cost management.
Shot
A shot refers to the amount of molten plastic material injected into the mould in a single cycle. The shot size must be carefully calculated to ensure the mould is completely filled without excess material, which can lead to defects and waste.
Mould
A mould is a hollow form or matrix into which the molten plastic is injected to create the desired part shape. Moulds are typically made of metal, such as steel or aluminium, and are precision-machined to meet exact specifications. They consist of two main parts: the cavity and the core.
Cavity
The cavity is the hollow portion of the mould that defines the outer shape of the moulded part. It is one half of the mould and is typically attached to the stationary platen of the moulding machine.
Core
The core is the counterpart to the cavity and forms the inner surfaces of the moulded part. It is the other half of the mould and is usually attached to the moving platen of the moulding machine. When the mould is closed, the core and cavity together form the complete mould shape.
Runner
A runner is a channel that guides the molten plastic from the injection nozzle to the cavities in the mould. The design of the runner system is essential for ensuring even distribution of the plastic and minimising waste.
Gate
The gate is the point at which the molten plastic enters the cavity of the mould. The design and location of the gate are critical for controlling the flow of material and preventing defects such as air bubbles or weld lines.
Sprue
A sprue is the primary channel through which the molten plastic is injected into the mould. It connects the injection moulding machine nozzle to the runner system. Once the part is ejected from the mould, the sprue is usually trimmed off and can often be recycled.
Understanding these basic terms is essential for anyone interested in the plastic injection moulding process. At Amey Plastics, we are committed to providing our clients with high-quality moulded products and sharing our knowledge to help you make informed decisions. Stay tuned for the next post in our series, Materials and Part Properties, where we will dive deeper into these more specific moulding terms and processes.
For more information or to discuss your injection moulding needs, contact the Amey Plastics team on 01730 266 525 or email sales@ameyplasticsltd.co.uk.
Comments