Exploring the Diverse Finishes of Plastic Injection Moulding
- ameyplasticstlc
- May 30, 2023
- 3 min read
One question that frequently comes up when we talk to customers is, what type of finishes are possible via the injection moulding process?
As you know, plastic injection moulding is a versatile manufacturing process widely used across various industries to produce high-quality plastic parts. While functionality and design are key considerations, the finish of the final product also plays a vital role. In this blog post, we will delve into the world of plastic injection moulding finishes and explore the different options available, and the variety might just surprise you.
1. Smooth and Glossy Finish: One of the most common finishes achieved through plastic injection moulding is a smooth and glossy surface. This finish is often desired for products that require an aesthetically pleasing appearance, such as consumer electronics, automotive components, and household appliances. It can be achieved by using a high-quality mould and utilising a polished tool surface.
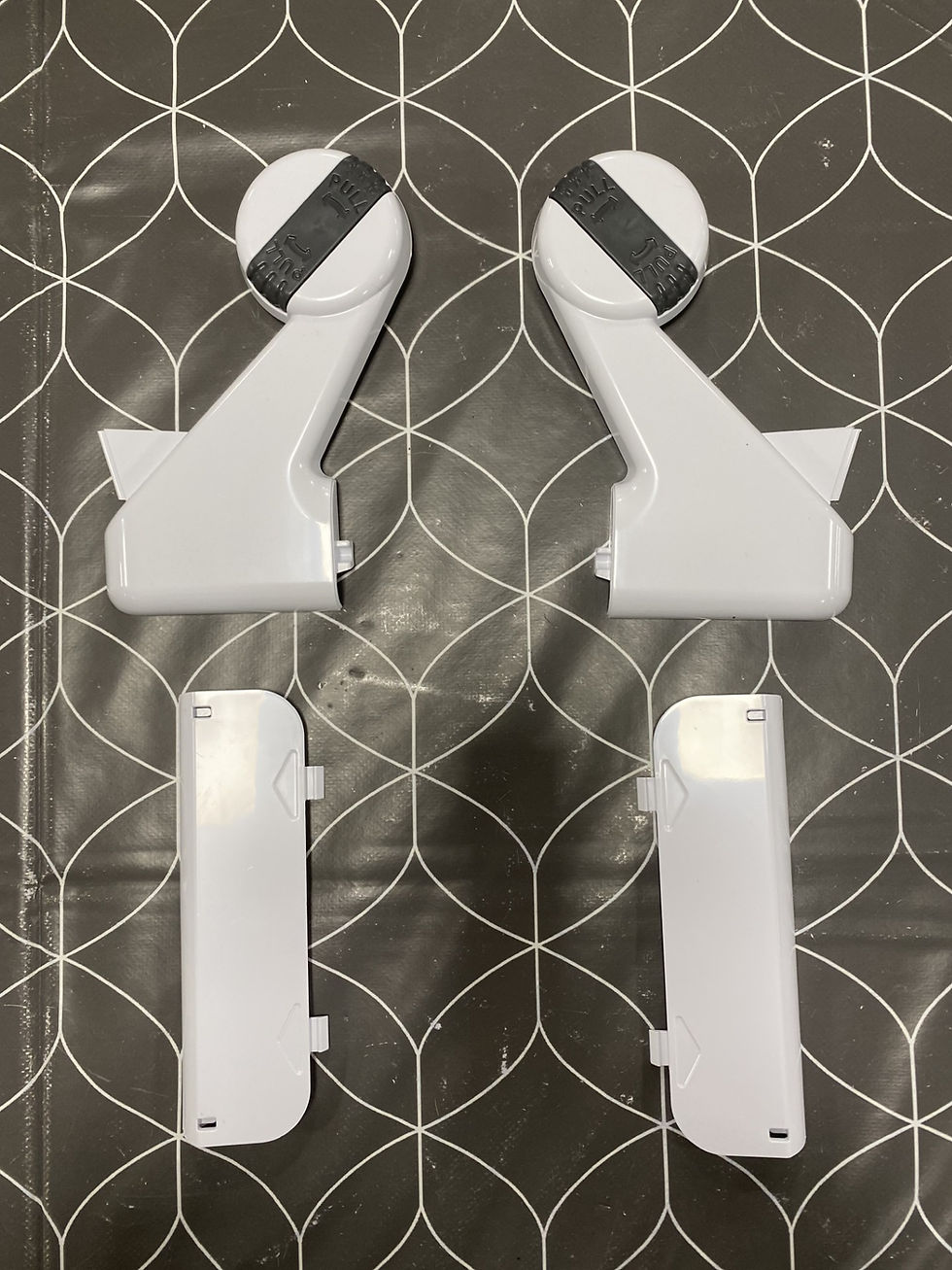
Glossy injection mould finish
2. Textured Finish: For applications that require enhanced grip or a unique visual appeal, a textured finish is employed. Texturing can be achieved through various techniques, including chemical etching, bead blasting, or using textured inserts in the mould. This finish is commonly found in items like tool handles, electronic casings, and household items.
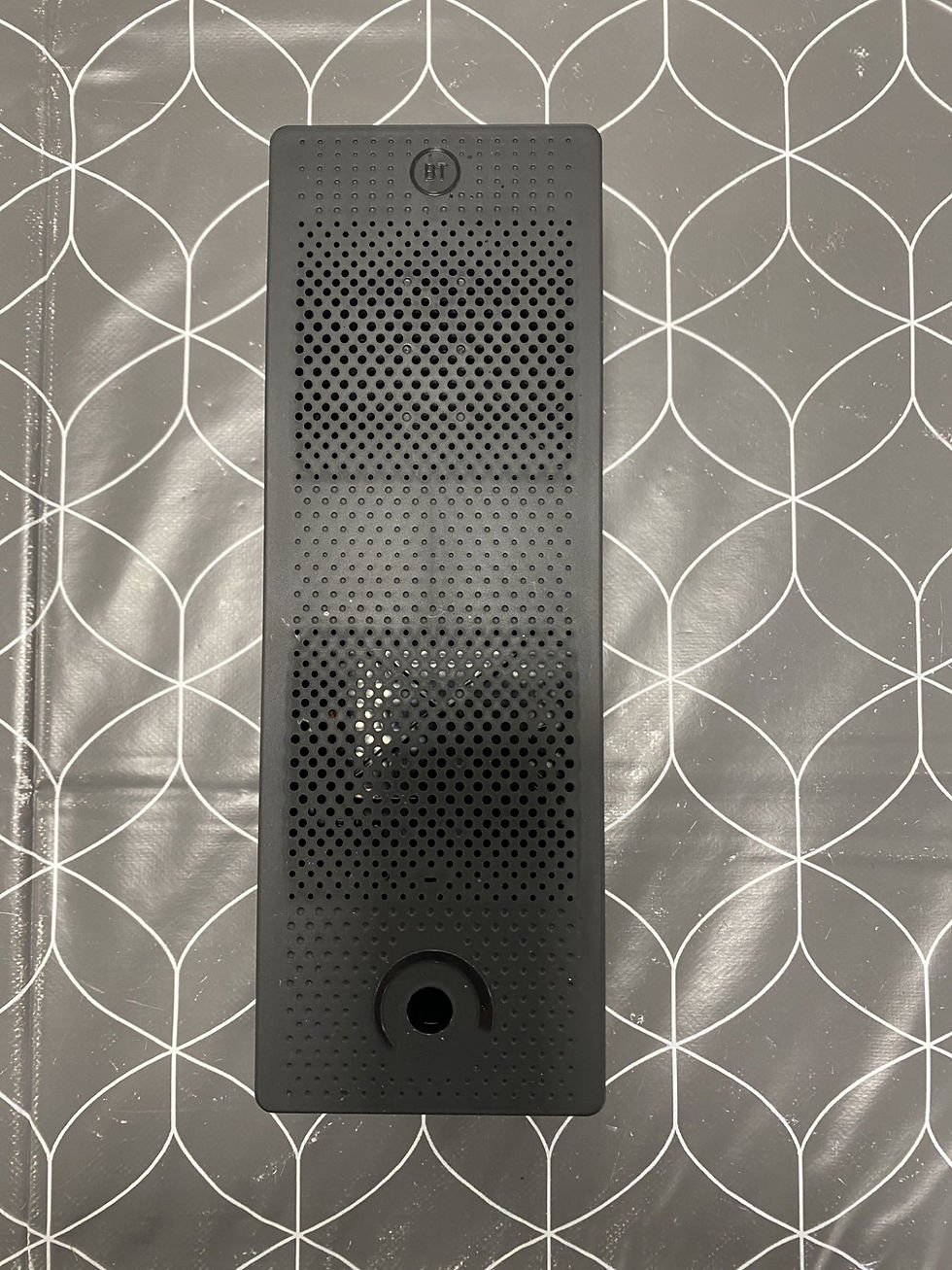
Textured injection mould finish
3. Matte Finish: Sometimes, a more subdued and non-reflective surface is desired. A matte finish can be achieved by modifying the mould surface or incorporating additives into the plastic material during the injection moulding process. This finish is commonly seen in products like laptop casings, cosmetic containers, and furniture components.

Matte injection mould finish
4. Metallic Finish: To mimic the appearance of metal, plastic parts can be given a metallic finish. This is achieved by applying specialised coatings to the moulded part, such as metal plating or painting techniques. The metallic finish is popular in automotive interiors, decorative trims, and consumer electronics.
5. Soft-Touch Finish: Certain applications require a tactile and soft feel. A soft-touch finish can be achieved by over-moulding a layer of thermoplastic elastomer (TPE) onto the rigid plastic component. This finish is commonly utilised in products like handles, grips, and medical devices where comfort and grip are crucial.
6. Customized Colours and Graphics: Plastic injection moulding offers endless possibilities for incorporating custom colours and graphics into the finished product. Through techniques like colour matching, colourants, and in-mould labelling, manufacturers can create parts that align with their brand identity or specific product requirements. This is particularly beneficial for consumer goods, toys, and promotional items.
The plastic injection moulding process not only enables the production of high-quality plastic parts but also offers a diverse range of finishes. From smooth and glossy to textured and soft-touch, manufacturers can achieve the desired aesthetic and functional characteristics for their products. Understanding the available options allows you to make informed decisions when it comes to selecting the appropriate finish for their specific applications.
Remember, the choice of finish depends on factors such as the intended use of the product, brand image, and customer preferences. By collaborating with an experienced injection moulding company, like Amey Plastics, you can leverage the full potential of plastic injection moulding to achieve the desired finish and create visually appealing and functional products.
If you’ve got a project that involves plastic injection moulded components that you’d like to discuss, please contact the Amey Plastics team on 01730 266525 or email sales@ameyplasticsltd.co.uk.
Comments