but what is a chiller used for?
Amey Plastics took delivery this month of our new state-of-the-art chiller, courtesy of ToolTemp, a manufacturer of temperature control equipment. The new 80kW unit provides greater reliability and increased energy-efficiency, particularly important in supporting our business objective to continue to become as sustainable a company as possible.
Whilst we are delighted with our new addition, not everyone is familiar with how a chiller works in the plastic injection moulding process. So, we thought we’d give you a brief overview of how this brilliant piece of equipment helps us in the injection moulding industry.
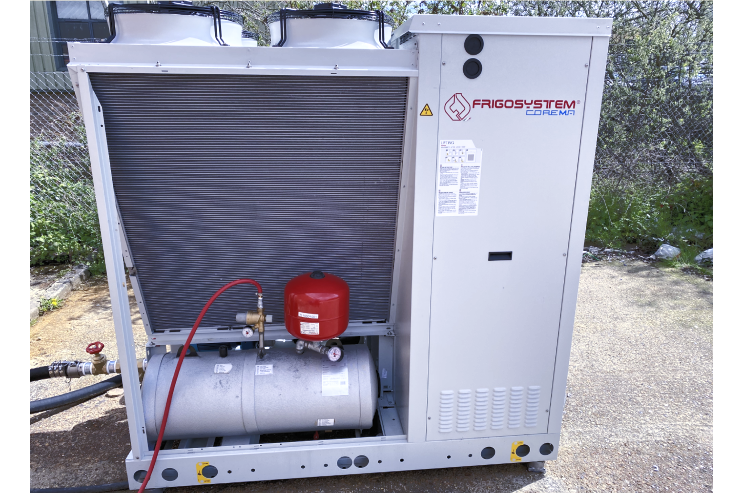
So, what does a chiller do in the plastic injection moulding process?
As you know, the plastic injection moulding process involves injecting molten plastic into a mould cavity to create a specific shape or part. During this process, it's essential to keep the mould at a consistent temperature to ensure the quality of the final product. This is where a chiller comes in.
A chiller is a refrigeration system that removes heat from a process and transfers it to another medium, usually air or water. In the plastic injection moulding process, the chiller cools the mould to a specific temperature before the molten plastic is injected.
The chiller works by circulating a refrigerant, such as R-410A or R-134a, through a closed loop system. The refrigerant absorbs the heat from the mould and carries it away to the chiller unit. Inside the chiller unit, the refrigerant releases the heat to the ambient air or a cooling tower. The cooled refrigerant then returns to the mould to remove more heat, and the cycle repeats.
There are two primary types of chillers used in plastic injection moulding: air-cooled and water-cooled. Air-cooled chillers use ambient air to cool the refrigerant, while water-cooled chillers use water from a cooling tower to remove the heat from the refrigerant.
Air-cooled vs Water-cooled chillers
Typically, air-cooled chillers are less expensive and more compact than water-cooled chillers, but they have a lower cooling capacity and are less efficient. Water-cooled chillers are more efficient and have a higher cooling capacity, but they require a cooling tower and a water supply.
What are the benefits of using a chiller?
In addition to keeping the mould at a consistent temperature, a chiller also helps to reduce cycle time, increase production rates, and improve the quality of the final product. By cooling the mould quickly and efficiently, a chiller can speed up the solidification process of the molten plastic, reducing the time it takes for the part to be ejected from the mould.
A chiller is an essential component in the plastic injection moulding process. It helps to ensure the quality and consistency of the final product while also increasing efficiency and production rates. We are delighted with our new chiller and are grateful to ToolTemp for helping us find the right one for our needs. If you have any plastic injection moulding requirements, contact the Amey Plastics team on 01730 266525 or email sales@ameyplasticsltd.co.uk.
Comments